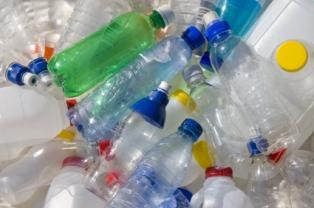
The recycled plastic process recovers scrap or discarded plastic and reclaims it into something new and useful. Most plastics are recyclable, but first they have to be separated into their polymer types. Plastics are separated according to their resin identification code, which were developed by the Society of the Plastics Industry in 1988. Manufacturers can voluntarily mark their products with the identification code. This makes it easier for consumers to recycle. Some municipalities require that households sort their plastics by code before leaving them out for curbside recycling.
Types of Plastics
- Type 1 is PET and PETE or polyethylene. Common applications of this plastic are soda and water bottles and peanut butter jars.
- Type 2 is HDPE or high density polyethylene. Common applications are milk and juice jugs and plastic bags for trash and shopping.
- Type 3 is PVC or polyvinylchloride. PVC piping and juice bottles are common applications of PVC.
- Type 4 is LDPE or low density polyethylene. Frozen food bags, and ketchup and mustard bottles are often made from LDPE.
- Type 5 is polypropylene of PP. Tupperware and disposable cups and plates are often made using polypropylene.
- Type 6 is PS or polystyrene. Common applications for PS are egg cartons and packing peanuts.
- Type 7 refers to all other types of plastic.
The most commonly recycled plastics are type 1, 2 and 6. These plastics are downcycled into other plastic items. Type 1 plastics are often turned into non-food containers. Type 2 plastics are used to make plastic lumber. Type 6 can be turned into trays, pens and insulation.
Challenges in the Recycled Plastic Process
The reason plastics must be separated by identification code is that plastics have a high molecular weight. In fact they are more difficult to recycle than glass and metal. Heat alone is not enough to dissolve plastic. The recycling process is easier when different types of plastic are not mixed together.
Another challenge in the recycled plastic process is the large amount of dyes, filler and other additives used in the plastic manufacturing process. Fillers are used make plastics pliable but they are very difficult to remove during recycling. Additives are used less frequently in plastic bags, which is why these items are recycled at higher rates.
Recycling Plastics
Despite the challenges, more and more plastic is being recycled every year. The amount of plastics that are recycled has increased every year since 1990. More than 1,800 U.S. businesses reclaim post-consumer plastics according to the American Plastics Council. Still, the United States only recycled about five percent of the plastics produced domestically.
Plastics are collected from curbside recycling bins and drop-off locations. From there, they go to a material recovery facility, where they are sorted and sent to a reclamation facility. At the reclamation facility, the plastic is inspected and washed. Next it is chopped into small flakes. The flakes are placed in a flotation tank and then dried in a tumbler. The dried flakes are placed in an extruder where they are melted. These extruders are expensive to operate. The melted plastic is sifted through a screen to remove any contaminants and then it is formed into strands. Finally, the strands are chopped into pellets and sold to manufacturers to make new products.
As new technologies are developed, the cost of the recycling plastic process will decrease and hopefully the amount of plastic recycled will increase. At the same time, consumers are becoming more aware of the impact of waste on the planet and they are working to reduce the use of plastic bottles and bags.